LiteTec by IAC approaches mass reduction through the use of alternative materials and innovative processes. These lightweight technologies meet safety, durability and functionality requirements all the while helping global automotive manufacturers meet emissions standards, reduce fuel consumption and extend the range for battery-electric vehicles.
LiteTec
CoreBack
IAC’s proprietary CoreBack injection molding process adds a chemical foaming agent to the resin when molding vehicle interior components. Once injected, the mold is opened to activate the foaming agent, creating a stronger product that is up to 30 percent lighter than conventional injection molded components.
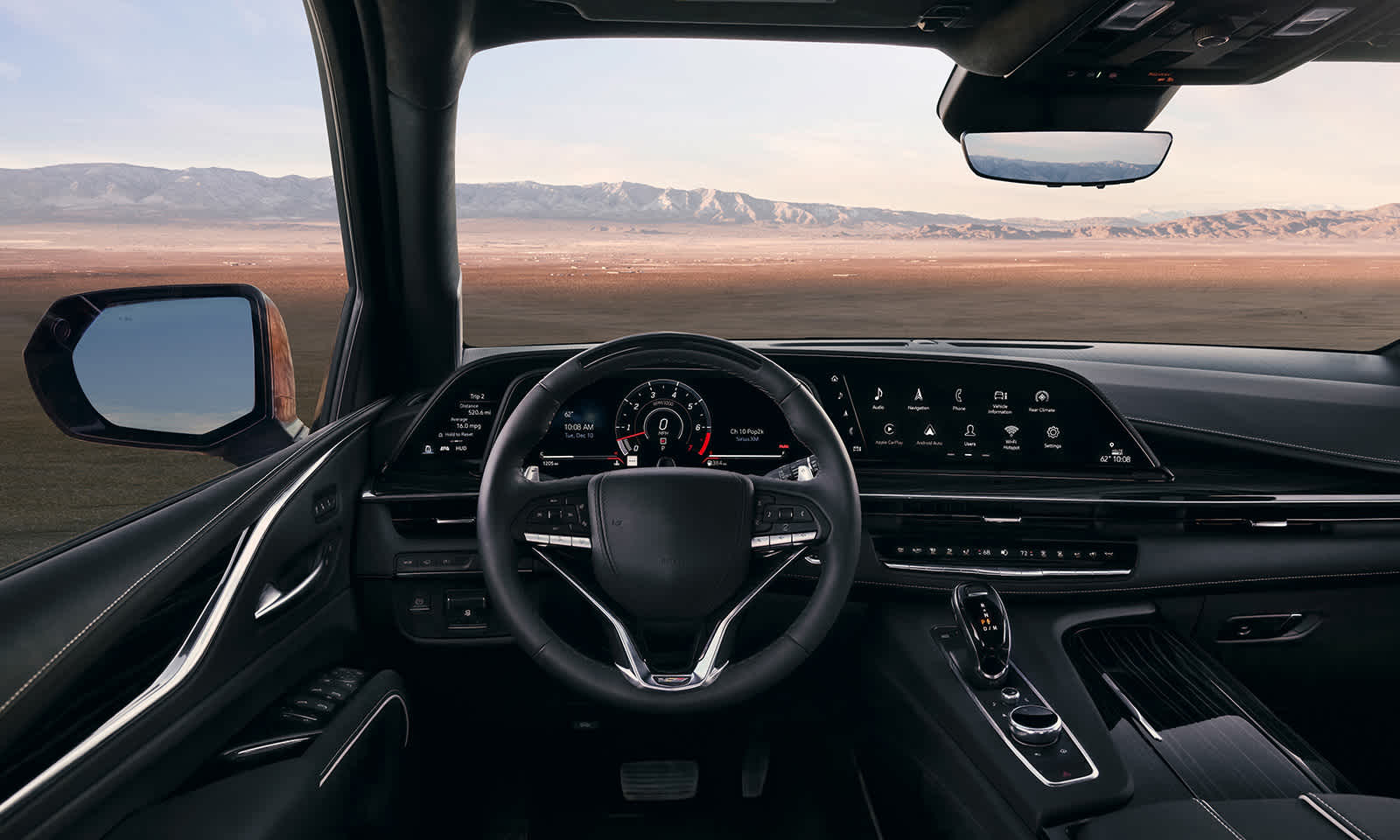
Injection Molded Soft Skin
IAC’s proprietary Injection Molded Soft Skin technology (IMSS) uses Hi-Flow TPE material to ensure consistent skin thickness at desired targets without heavy corners and improved design capabilities. Compared to alternative production processes, IMSS offers improved fit-and-finish while still eliminating porosity concerns. IMSS has increased sustainability with improved chemistry, lower weight, significantly reduced carbon footprint and less emission/VOCs versus PVC slush skins.
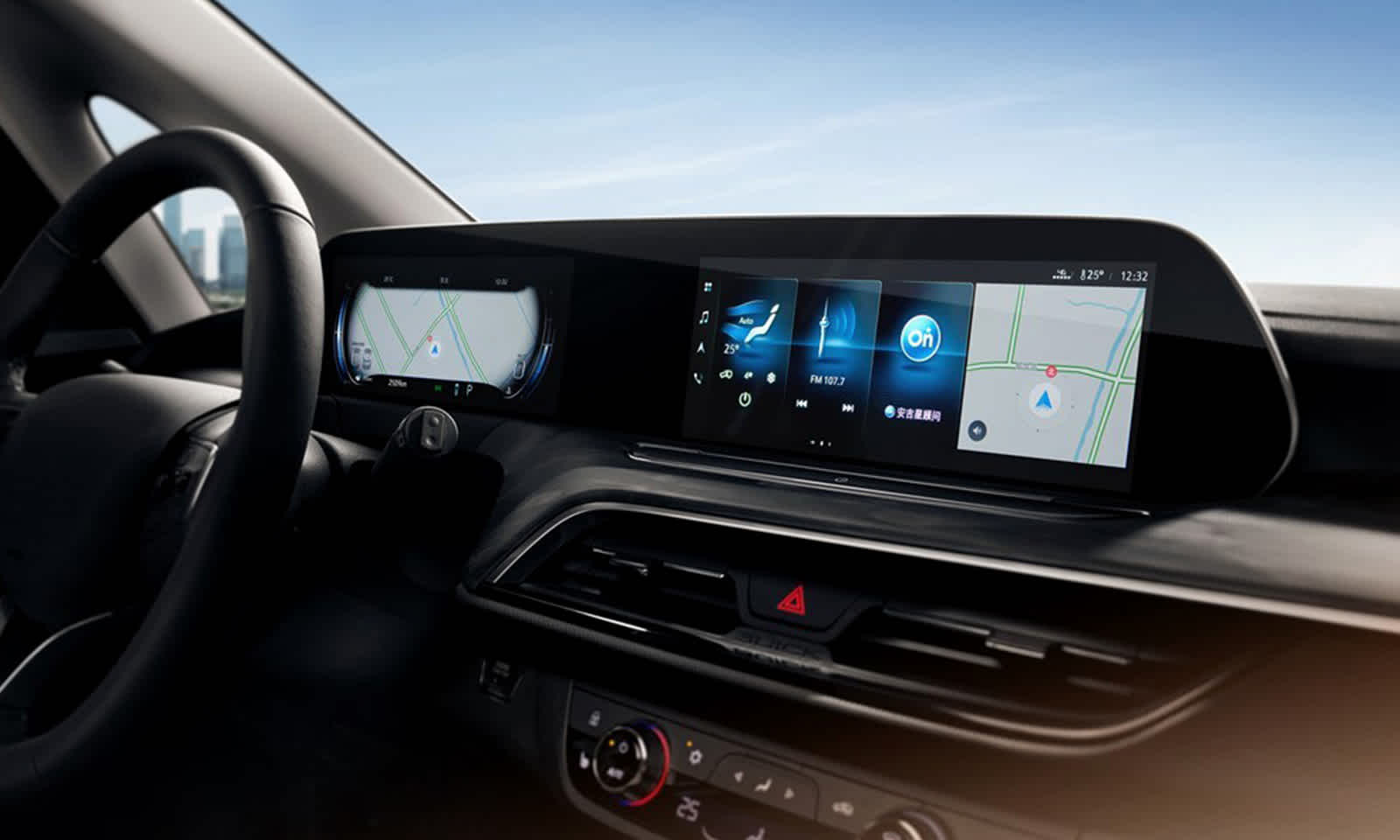
Natural Fiber Materials
IAC uses natural fibers to provide a renewable, sustainable reinforcement that strengthens plastics. Often used in IAC's hybrid technologies, natural fiber reinforcements can be used across the company's portfolio, including in headliners, doors, instrument panels and consoles.
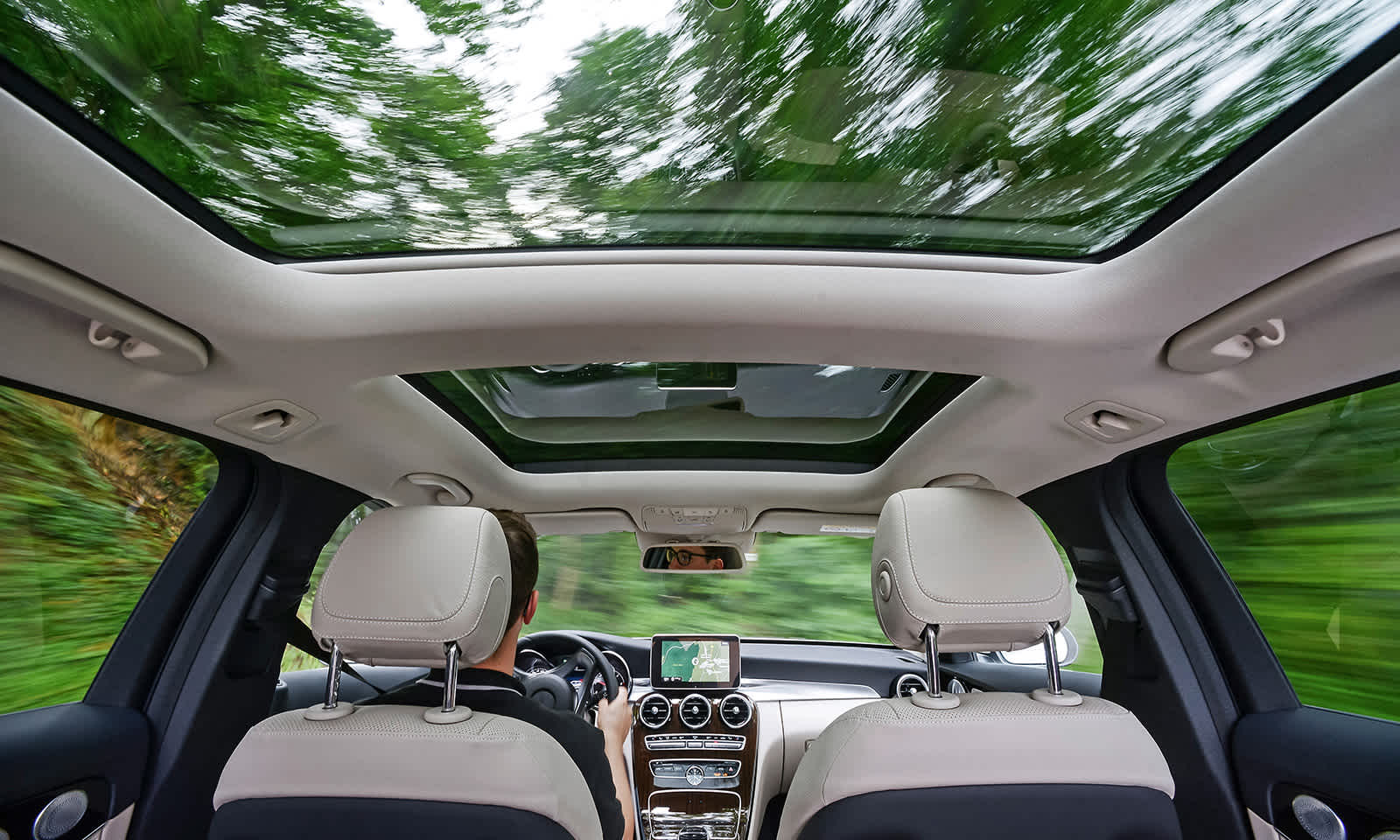